The Power of Plastics Molding in Modern Business
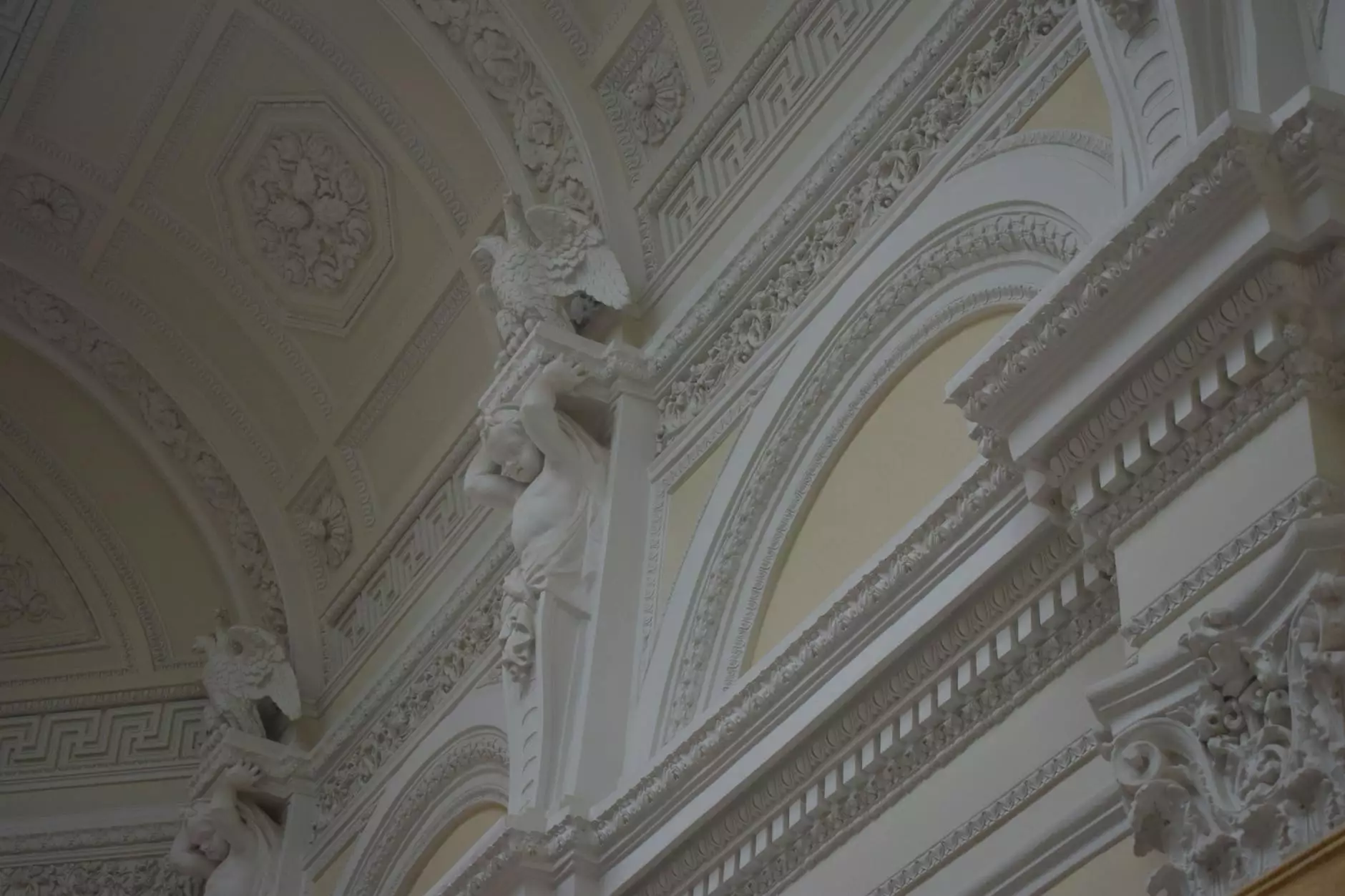
In today’s fast-paced industrial landscape, the importance of plastics molding cannot be overstated. This versatile manufacturing process plays a pivotal role in the production of a wide array of products across various sectors. From automotive components to consumer goods, plastics molding enables businesses to bring their vision to life efficiently and cost-effectively. In this article, we will delve into the intricacies of this technology, its benefits, and its far-reaching implications for industries worldwide.
What is Plastics Molding?
Plastics molding refers to a set of processes used for shaping plastic materials into desired forms. The most common methods include injection molding, blow molding, rotational molding, and extrusion. Each technique serves unique purposes and is chosen based on the specific requirements of the product being manufactured.
1. Injection Molding
Injection molding is by far the most prevalent plastics molding method. In this process, plastic material is heated until it melts and is then injected into a mold cavity where it cools and solidifies into the final product. This method is ideal for producing high volumes of identical items quickly and with great precision.
Applications of Injection Molding
- Automotive Parts: Components such as dashboards, gear knobs, and bumpers.
- Consumer Products: Items like containers, toys, and kitchen utensils.
- Medical Devices: Tools and components that require stringent cleanliness and precision.
2. Blow Molding
Blow molding is used primarily for creating hollow plastic products. The process involves inflating a molten tube of plastic into a mold to form containers, bottles, and other hollow shapes. This method is especially favored in the beverage and packaging industries.
Applications of Blow Molding
- Beverage Bottles: Producing lightweight, durable bottles for drinks.
- Automotive Fuel Tanks: Creating complex shapes for effective fuel storage.
- Household Containers: Storage solutions for various household items.
3. Rotational Molding
In rotational molding, powdered plastic is placed in a mold that is rotated on two axes simultaneously. This allows the plastic to cover the interior of the mold evenly, creating consistent wall thickness. This method is excellent for manufacturing large, hollow items.
Applications of Rotational Molding
- Industrial Containers: Tanks and bins used for storage.
- Outdoor Furniture: Durable and weather-resistant pieces.
- Playground Equipment: Safe, sturdy components for children's play.
4. Extrusion
Extrusion involves pushing melted plastic through a die to create long, continuous shapes such as pipes, sheets, or profiles. This method is prevalent for producing products that require uniform cross-sections.
Applications of Extrusion
- Pipes: Used in plumbing and irrigation systems.
- Films and Sheets: For packaging and protective coverings.
- Profile Shapes: Custom shapes for various industrial applications.
The Advantages of Plastics Molding
Adopting plastics molding technology can deliver a myriad of benefits to businesses looking to innovate and improve their production capabilities. Here are some of the most notable advantages:
Cost Efficiency
One of the primary benefits of plastics molding is its cost efficiency. The ability to produce large quantities of products quickly reduces the cost per item significantly. This is particularly beneficial for businesses aiming to minimize production costs while maximizing output.
Versatility
Plastics molding offers unparalleled versatility. The processes can be adapted to create a wide range of products in varying shapes, sizes, and materials. This adaptability allows businesses to respond quickly to market demands and customize their offerings based on customer needs.
Precision and Consistency
The precision of plastics molding techniques ensures high-quality products with minimal defects. Injection molding, for example, can create components with extremely tight tolerances, making it suitable for industries that require strict quality control, such as aerospace and medical manufacturing.
Reduced Waste
Unlike traditional manufacturing methods, plastics molding generates less waste material. The efficiency of the molding process means that the majority of the plastic utilized is converted into finished products, leading to a more sustainable production approach.
Plastics Molding in Various Industries
The reach of plastics molding extends across numerous industries, each benefiting from this transformative technology. Let us explore how different sectors leverage plastics molding to enhance their operations and products.
Automotive Industry
The automotive sector relies heavily on the plastics molding process to produce lightweight, durable parts that improve fuel efficiency and reduce emissions. With the advent of electric vehicles and the demand for innovative designs, the need for advanced plastics molding techniques is greater than ever.
Consumer Goods
In the realm of consumer products, plastics molding is fundamental in designing and manufacturing everything from simple household items to sophisticated electronics casings. The flexibility in design allows brands to create products that stand out in a crowded marketplace.
Medical Sector
The medical industry benefits from the high precision and hygiene standards achievable through plastics molding. Disposable syringes, surgical instruments, and various medical devices are produced using molds that ensure sterility and accuracy, essential for patient safety.
Packaging Industry
Packaging is another area where plastics molding shines. The ability to create various container shapes and sizes efficiently is crucial for food, beverage, and pharmaceutical industries. Sustainable packaging solutions are also increasingly being developed through innovative molding techniques.
Choosing the Right Plastics Molding Partner
When considering plastics molding for your business, selecting the right partner is vital. Here's what to look for:
Experience and Expertise
Ensure your chosen partner has extensive experience in plastics molding. Look for a company that has a proven track record in your specific industry, as they will better understand your needs and requirements.
Technology and Capabilities
The best partners utilize the latest technologies and molding techniques. They should be capable of handling various types of molds and materials to cater to your specific product needs.
Quality Assurance
A commitment to quality assurance is essential. Your partner should have established quality control systems in place to ensure every product meets the highest standards.
Customer Service and Support
Finally, strong customer service is essential. Your molding partner should be responsive and willing to work closely with you throughout the design and production process.
Conclusion
In conclusion, plastics molding is an indispensable technology in the modern business landscape, driving innovation across numerous industries. Its ability to produce high-quality, precise, and cost-effective products makes it an attractive solution for manufacturers worldwide. Companies looking to enhance their production capabilities would do well to embrace this transformative technology. With the right partner, businesses can harness the full potential of plastics molding to propel their growth and success forward.
For more insights and expertise in plastics molding, visit us at deepmould.net and discover how we can help you unlock new opportunities for your business.