Understanding the Role of a **Plastic Mold Manufacturer** in Modern Industry
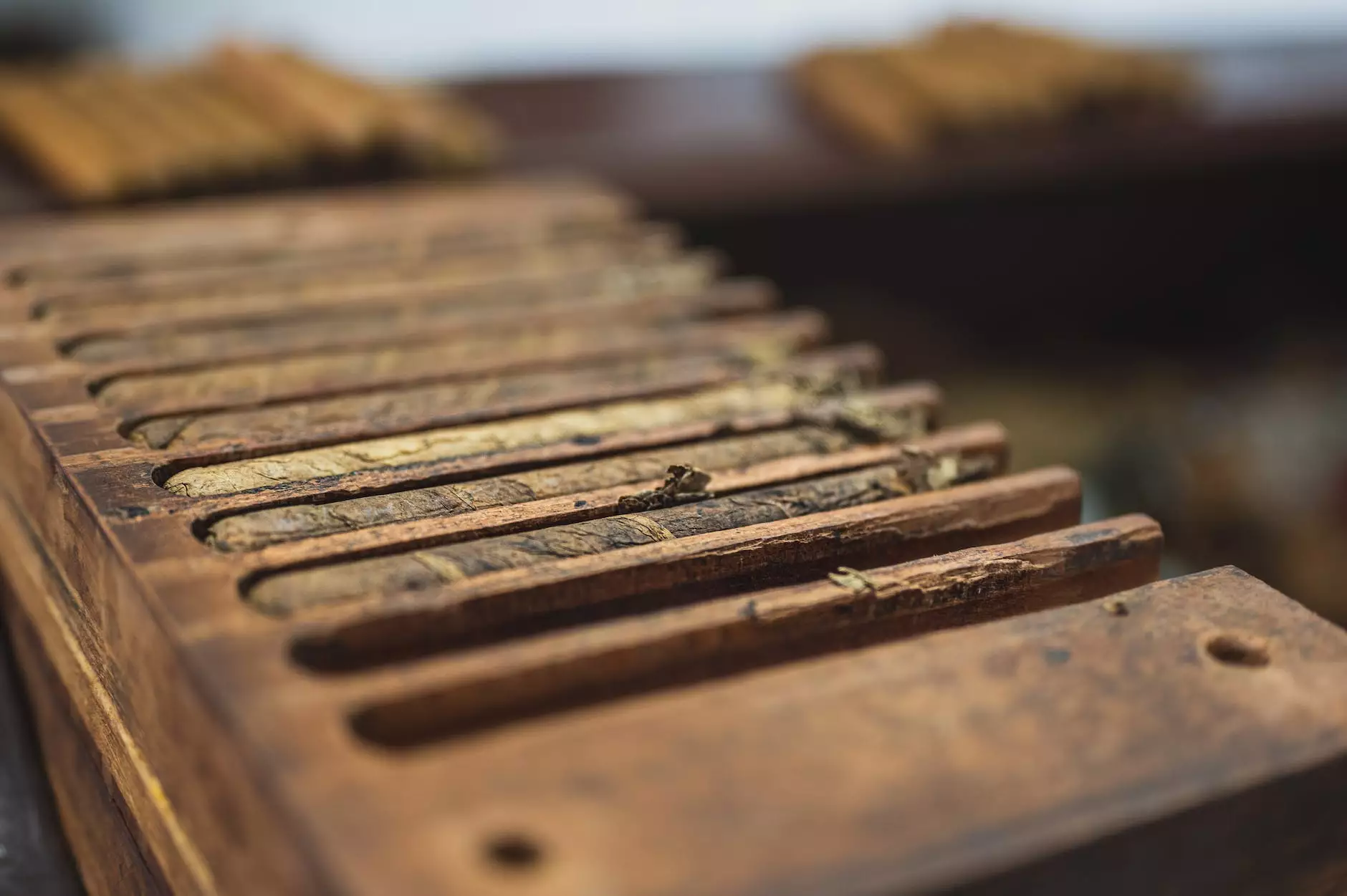
The manufacturing sector is a cornerstone of the global economy, and within this realm, plastic mold manufacturers play a pivotal role. As we delve into the intricacies of plastic molding, we'll explore the processes, technologies, and benefits that establish Hanking Mould as a premier plastic mold manufacturer. This guide will also provide insights to help businesses understand the best practices and innovations in the plastic mold-making industry.
What is Plastic Molding?
Plastic molding encompasses a variety of manufacturing processes that transform raw plastic materials into finished goods. This process is essential for industries ranging from automotive to consumer goods, allowing for mass production of high-quality plastic components. The most common method employed by plastic mold manufacturers is injection molding, which will be discussed in detail later. However, several other processes also exist, including:
- Blow Molding: Ideal for producing hollow plastic products.
- Compression Molding: Used primarily for thermosetting plastics.
- Rotational Molding: Suitable for large items with uniform thickness.
- Thermoforming: Involves heating plastic sheets to form various shapes.
The Importance of Plastic Mold Manufacturers
Plastic mold manufacturers are crucial in developing a wide array of products that consumers use every day. The ability to produce durable and precise molds directly influences product quality, production timelines, and cost-efficiency. Here are several reasons why choosing the right manufacturer matters:
- Quality Assurance: A reputable manufacturer ensures products meet stringent quality standards.
- Customization: Manufacturers can tailor molds to specific needs, ensuring unique solutions for specific applications.
- Cost Efficiency: Efficient production techniques reduce waste and lower costs.
- Innovative Solutions: Advanced technologies enable innovative mold designs that enhance functionality.
The Process of Plastic Injection Molding
One of the most efficient and widely utilized methods of plastic molding is injection molding. Here’s a detailed look at how the process works:
1. Design and Prototyping
The first step in the injection molding process is to create a design for the part. This involves:
- Utilizing CAD software to develop a 3D model of the component.
- Conducting simulations to test the design’s efficiency before production.
2. Mold Creation
Once the design is finalized, the next step is creating the mold, which involves:
- Machining the mold components from high-quality steel or aluminum.
- Assembling the mold and ensuring it fits correctly to prevent leaks during injection.
3. Material Selection
Choosing the right plastic material is crucial. Plastic mold manufacturers typically offer a wide range of materials, including:
- Polyethylene (PE)
- Polypropylene (PP)
- Polyvinyl Chloride (PVC)
- Polystyrene (PS)
- Thermoplastic Elastomers (TPE)
4. Injection Process
During the injection process, plastic pellets are fed into a heated barrel, where they are melted and injected into the mold at high pressure. This ensures that the mold is completely filled and forms the desired shape. The steps involved are:
- Melting plastic pellets to create a viscous material.
- Injecting the melted plastic into the mold cavity.
- Allowing the material to cool and solidify to form the final product.
5. Finishing and Quality Control
After the plastic has cooled and solidified, the mold is opened, and the part is ejected. It undergoes various finishing processes, such as:
- Trimming excess material.
- Surface finishing for aesthetics.
- Quality control checks to ensure dimensional accuracy.
Advantages of Using a Plastic Mold Manufacturer like Hanking Mould
Partnering with a specialized plastic mold manufacturer offers numerous advantages:
1. Expertise in the Field
With years of experience, Hanking Mould brings unparalleled expertise to the table. A knowledgeable team can spot potential issues before they arise and propose effective solutions, ensuring smooth production.
2. Access to Advanced Technology
We leverage cutting-edge technology to enhance the efficiency and quality of our molds that most DIY methods cannot match. Our state-of-the-art equipment allows us to create precise molds faster than traditional methods.
3. Comprehensive Customer Support
From initial consultation to after-sales support, our dedication to customer satisfaction is unwavering. Clients receive updates throughout the process, ensuring they remain informed at every stage.
Key Considerations When Choosing a Plastic Mold Manufacturer
Selecting a plastic mold manufacturer is a critical decision that can have lasting impacts on your business. Here are some key considerations:
1. Quality of Materials
Assess the types of materials the manufacturer uses. High-grade materials are essential for producing durable and long-lasting molds.
2. Production Capabilities
Evaluate the manufacturer's capabilities to handle the scale of your production needs, including their capacity for rapid prototyping and short lead times.
3. Customization Options
Determine if they offer customization options that align with your specific requirements, as this can help differentiate your products in the market.
4. Certifications and Standards
Check if the manufacturer adheres to industry standards, as certifications can reflect their commitment to quality and safety.
Case Studies: Successful Projects by Hanking Mould
At Hanking Mould, we have successfully collaborated with a wide range of industries, showcasing our versatility and expertise. Here are a few examples:
1. Automotive Industry
We developed a series of precision-engineered components for a leading automotive manufacturer. Our plastic molds allowed for the rapid production of complex parts while maintaining stringent quality standards.
2. Consumer Electronics
Our team created molds for several consumer electronics devices, enhancing their design and functionality. Our innovative solutions significantly reduced production costs and time to market.
Conclusion
In conclusion, the role of a plastic mold manufacturer cannot be overstated. With advancements in technology and processes, manufacturers like Hanking Mould are at the forefront of delivering high-quality, efficient, and customized solutions that cater to the diverse needs of different industries. Whether you're looking for a partner for your next product line or seeking insights into plastic mold manufacturing, understanding the intricacies and benefits of this industry is crucial for making informed decisions.
Choose Hanking Mould for your plastic mold manufacturing needs and experience the difference in quality, efficiency, and innovation.